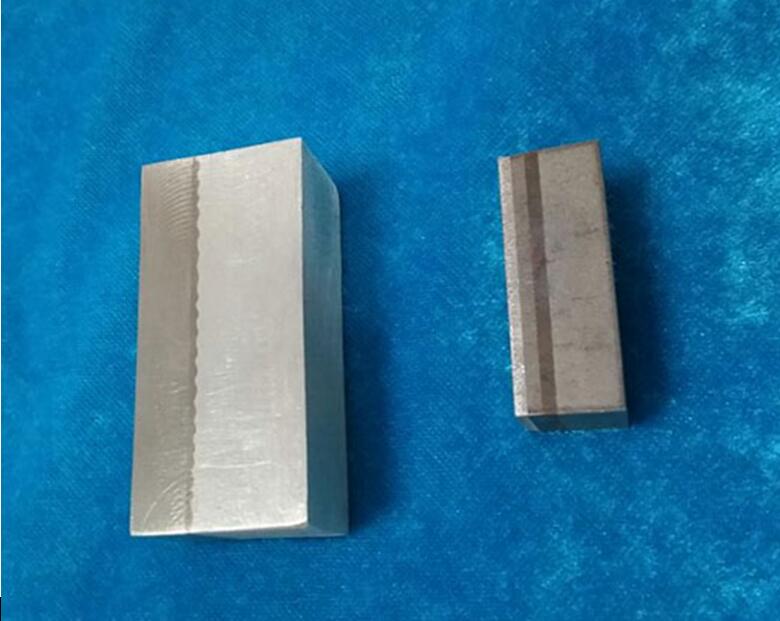
One is serious corrosion. Riveting connection cannot completely solve the problem of dissimilar metal corrosion between aluminum and steel. The long-term corrosion between the aluminum plate and the steel plate will cause corrosion of different kinds of metal on the aluminum plate and rivets, and some aluminum plates will be rotten, so they must be replaced regularly. The second is poor water tightness. From the first moment of material blanking, ships have to endure various forces. The hull is subject to the impact of waves and deformation caused by various internal and external forces all the year round. The aluminum rivets are easy to loosen, and the water tightness of the cabin is difficult to guarantee. Way to connect. Due to the significant difference in physical properties between aluminum alloy and steel and the metallurgical incompatibility between the two metals, it is difficult to achieve an effective connection between the two directly by welding. The steel transition plates made by Chalco Aluminum through the explosive compounding method provide a technical basis for welding the aluminum alloy superstructure and the main steel hull. With the increase in the number of high-performance ships built year by year, more and more ship superstructures use aluminum alloy structures, and the connection between the aluminum alloy superstructure and the steel hull uses steel transition plates, and the connection through welding is gradually replacing the traditional riveting. Connection process. Steel transition plates mainly have two combinations of aluminum aluminum steel or aluminum titanium steel. In explosive production of composite materials, a thin process plate is usually added between aluminum alloy and steel plate. This layer of thin plate can be made of pure aluminum or pure titanium. The aluminum-aluminum-steel composite material can be made of various grades of alloys in the AMg series, but due to the poor composite performance of the AMg series alloy plate and the pure titanium plate, the explosive composite material of aluminum-titanium steel is generally used at home and abroad AMn series alloys can be used as three-layer one-time explosive compounding and three-layer two-time explosive compounding as a multi-layer aluminum plate aluminum-steel explosive compound material. Aluminum-aluminum-steel generally adopts three-layer explosive compounding at one time. The interface of the aluminum-steel composite plate is not easy to form a wave-like bond, but forms a hybrid combination of direct bonding and wave-like bonding. In the explosive compounding of aluminum and steel, a metallurgical reaction occurs at the interface, resulting in brittle intermetallic compounds. As the charge density increases, the amount of melting of the interface matrix metal increases, and the generated intermetallic compound becomes more continuous, and its thickness increases slightly, and the shear strength of the composite interface is significantly reduced; the explosive welding process affects the diffusion of the aluminum-steel composite interface Not obvious. In the explosive welding of aluminum-steel, it is advisable to use small-volume welding to improve the strength of the explosive clad plate to overcome the boundary effect. Generally, the size of the clad material is 50-100mm wider than the base layer, and the transition joint must pass through 100% of the plate surface. Ultrasonic inspection, the combination rate must reach 100% before it is qualified. The use of explosive composite materials to achieve transitional connection between aluminum alloy and steel through welding has high production efficiency, and more importantly, the high strength of the connection part, good water tightness, and good corrosion resistance. These are unmatched by the riveting process.