"Copper clad aluminum bus for power transmission and transformation equipment" marks that copper clad aluminum materials have entered a new development period in the power industry. At present, copper aluminum composites used in the electrical industry mainly include: copper clad aluminum wire, copper clad aluminum bus bar and copper clad aluminum transition joints.
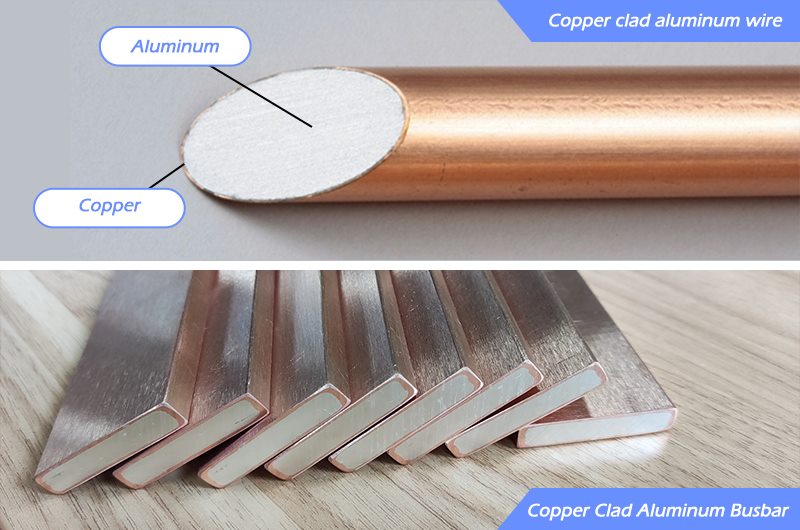
1. copper clad aluminum wire
The conductor has "skin effect" when transmitting AC power. The current distribution inside the conductor is uneven. Most of the current is concentrated on the surface of the conductor, and the internal current is very small. Replacing aluminum wire with copper clad aluminum wire can reduce the AC transmission resistance and improve the mechanical properties of the material; Replacing copper wire with copper clad aluminum wire can save copper resources and reduce the quality of wire. Generally, the volume ratio of copper and aluminum in copper clad aluminum wire is 10:90 or 15:85. At present, the preparation methods of copper-clad aluminum composite wire mainly include cladding welding, rolling and crimping, hydrostatic extrusion and core filling continuous casting.
2. copper clad aluminum busbar
The main difference between copper clad aluminum busbar and copper clad aluminum wire rod lies in their different cross-sectional shapes. The former is rectangular cross-section, and the latter is circular cross-section. Copper aluminum composite bus is a kind of copper aluminum binary metal composite material, which is used as the power transmission conductor of power transmission and transformation equipment. Its surface is copper and its inner core is aluminum. The two are in the metallurgical combination state, ensuring the electrical, mechanical processing and safety performance of the product. Copper clad aluminum busbar comprehensively utilizes the corrosion resistance and electrical characteristics of copper and the advantages of low density and easy processing of aluminum, thus improving the cost performance and construction convenience. Generally, the volume ratio of copper layer in copper clad aluminum busbar shall not be less than 18%. The main preparation processes of copper-clad aluminum busbar include rolling and crimping, hydrostatic extrusion and core filling continuous casting.
3. copper clad aluminum transition joints
When the transmission line and electrical equipment involve the connection of both ends of copper and aluminum, the copper clad aluminum transition joints is a crucial part. If copper aluminum materials are directly overlapped without using copper aluminum composite joints, there will be a micro gap on the contact surface of copper aluminum materials. When the contact surface is exposed to the air, copper, aluminum and the air in the contact gap will form a primary cell and generate electrochemical corrosion, which will lead to electrical faults such as phase break, short circuit and power failure.
When copper clad aluminum transition joints are used to connect the two ends of copper and aluminum, the copper and aluminum bimetals achieve atomic level combination, eliminating the gap between the two metals, thus avoiding the occurrence of electrochemical corrosion. The main preparation methods of copper aluminum composite joints include friction stir welding, explosive welding, pressure welding, diffusion welding and brazing.