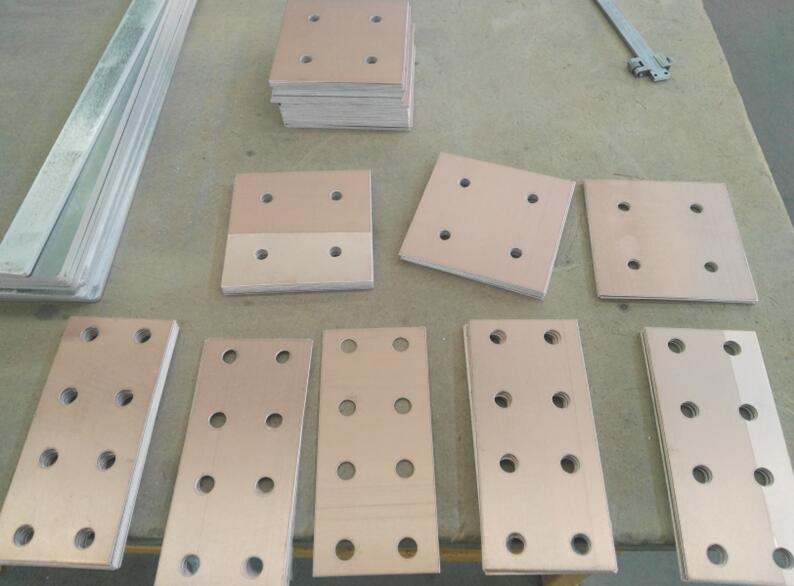
The mechanical properties include interface bonding strength, tensile strength, bending strength and microhardness. Interface bonding performance is an important index to measure the composite effect of bimetal composite, usually by stripping, stretching and shearing.
After the current is applied, copper aluminum bimetallic transition inserts "skin effect makes it have higher conductivity than single pure aluminum, especially when the frequency of current exceeds a certain value, the current passes through the surface basically, and the conductivity of copper / aluminum bimetal composite is similar to that of pure copper. The physical parameters describing the electrical properties of Cu / Al bimetal composite include resistance, resistivity, impedance, current density and conductivity. The presence of intermetallic compounds at interface will harm the conductivity of copper / aluminum bimetal composites. Therefore, in the process of preparing copper / aluminum bimetal composites, the thickness of intermetallic compounds can be reduced properly to improve the conductivity of the composite materials on the basis of ensuring the mechanical properties of the composite.
The results show that the measured thermal conductivity is less than the theoretical thermal conductivity, which mainly includes three aspects: (1) the interface between the matrix metal has grain boundary and other defects, which results in thermal resistance and reduces the thermal conductivity(2) The interface between the base metal will cause scattering effect on the electron, and the thermal diffusion coefficient will be reduced(3) The surface of the composite materials will consume a certain pulse energy and the heat transfer will weaken. Zhang found that vacancy, dislocation and dislocation clusters are introduced in the preparation of bimetal composites, which hinder the free movement of electrons, increase the probability of electron heat dissipation, increase the thermal resistance of the composite materials, and the thermal conductivity is lower than that of the base metal. The thermal conductivity of the intermetallic compounds in the interface of Cu / Al bimetal composites also affects their thermal conductivity. On the other hand, temperature is an important factor affecting the thermal conductivity of bimetal composites. The scattering mechanism of thermal conductivity is different in different temperature range. The thermal conductivity in the low temperature region is mainly affected by lattice defects, and the thermal conductivity in the high temperature region is mainly affected by phonon.
Cooper aluminum bimetallic transition inserts are widely used in power systems, such as lithium-ion batteries, radiators, etc., which requires strong corrosion resistance. Due to the different service environment of copper / aluminum bimetal composite, there are also differences in corrosion media, and the corresponding research focuses are different. Among them, the corrosion medium includes acid, alkali, salt, water vapor and solid particles. In the actual service, bimetal composite materials may suffer simultaneously
Cooper aluminum bimetallic transition inserts are widely used in power, air conditioning, new energy vehicles, Kitchenware and other fields, and its comprehensive performance advantages are obvious. With the expansion of market demand for copper / aluminum bimetal composite, new technology needs to be developed continuously to expand product types and enhance market competitiveness.