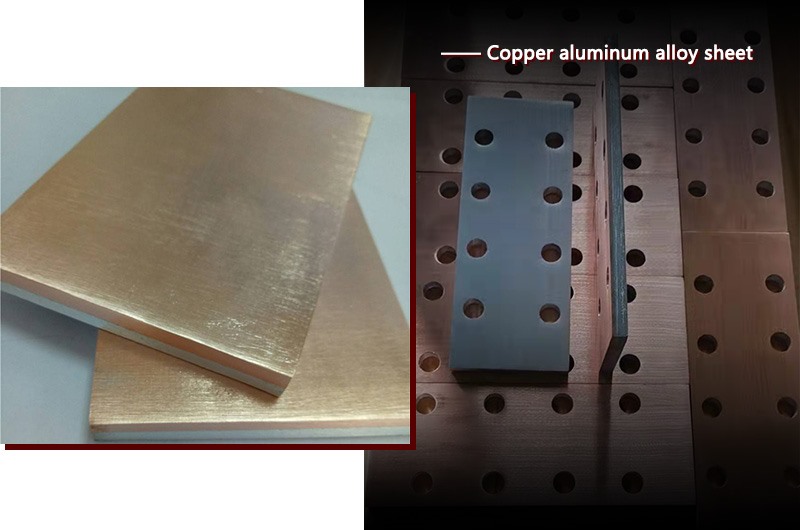
Chalco Aluminum adopts advanced heat treatment process of copper-aluminum composite materials, controls diffusion annealing temperature, holding time and eliminates defects such as surface bubbling, which effectively ensures that the material can withstand the increased temperature difference, thermal expansion and contraction. Hole, bending, no cracking, no separation, and the interface bonding strength is continuously enhanced in the subsequent use process.
The annealing process can be effectively adjusted according to different composite material specifications (thickness, width, etc.) to achieve the best performance of the material. When the thickness increases, the annealing temperature and annealing time approach the upper limit; when the thickness decreases, the annealing temperature and annealing time approach the lower limit. When the width of the composite strip material increases, the annealing temperature and annealing time approach the upper limit; when the width of the composite strip material decreases, the annealing temperature and annealing time approach the lower limit. Copper aluminum alloy sheet, through the above annealing process, realizes the transition from physical bonding to metallurgical bonding of the interface. It can be seen from the SEM photos of the peeling interface of copper aluminum sheet through experiments that the composite interface obtained by the above heat treatment process is too late to form intermetallic brittle compounds.
Thus, the composite effect of the interface is guaranteed. In order to achieve the effect of annealing strengthening: the bending performance of the material is improved, the shear strength of the composite interface is increased, and the composite material can also obtain a certain hardness value.