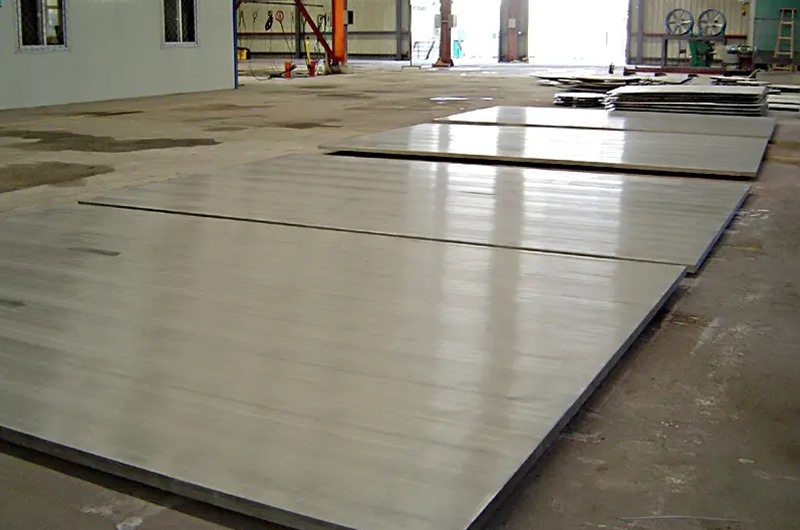
In recent years, Ti Al explosive welded clad plates have attracted much attention. Through certain processing technology, titanium and aluminum are made into layered composites, which have the characteristics of corrosion resistance, high temperature resistance and impact resistance of titanium; It also has the characteristics of low specific gravity of aluminum, good heat conduction and conductivity, and low cost.
Explosive welding is one of the main processes for preparing layered composite materials. It uses the energy generated by explosive explosion on the surface of the upper metal plate to convert into the energy of the upper metal plate movement, so that the upper metal plate will collide violently with the substrate placed on the lower layer in the process of high-speed movement, so that the composite plate and the substrate can be combined. The Ti Al explosive welded interface is a transition zone for the composition, structure, performance and energy of titanium and aluminum dissimilar materials, and a new bond connecting two kinds of materials. Under the action of detonation wave, the composite plate collides with the substrate at a high speed, causing instantaneous high temperature, high pressure and large shear strain near the interface. Heterogeneous materials achieve high-strength bonding under this extreme condition.
With the size of 1050mm × 650mm × 1mm TA1 titanium plate is multi-layered, with a size of 1000mm × 600mm × Ti Al explosive welded clad plates were prepared by explosive welding with 3mm al-1060 aluminum plate as the base. Explosion welding adopts the method of parallel installation, and ammonium nitrate mixed explosive is selected. The density is 790kg/m3, the theoretical explosion speed is 2400m/s, the charge ratio is 0.83, and the gap between the base and the clad plate is 4mm. From the physical process of explosive welding, after detonation, the clad plate and the substrate collide at a high speed, causing severe plastic deformation on the joint surface, increasing the internal energy of the material, and the air between the base and clad plate is adiabatic compressed under high pressure to generate heat. Under the combined action of the two, the interface temperature rises, causing the melting of the interface metal micro area. However, the titanium side and aluminum side far away from the interface are infinite cooling sources, and the molten metal is rapidly cooled, The heating and cooling rates at the interface are very high.
1) Ti Al clad plates did not realize recombination at the initiation point due to the effect of explosive rarefaction wave, resulting in boundary effect. Along the detonation direction, the shape of the interface bonding zone changes from flat bonding to waveform bonding, and there are molten blocks in the wave front. XRD shows that the molten blocks are TiAl3 intermetallic compounds.
(2) EBSD analysis shows that the grain refinement occurs at the titanium / aluminum interface, which is due to the high-speed impact between the clad plate and the substrate. The interface temperature rises sharply and then decreases. The cooling rate can reach 108k/s, and the interface undercooling is great, which promotes the increase of nucleation rate, resulting in the refinement of interface grain. EBSD strain diagram shows that the strain near the interface is the largest, and the strain gradually weakens with the increase of the distance from the interface.
(3) SEM showed that there was an obvious diffusion layer at the titanium / aluminum interface. EDS line scanning showed that titanium and aluminum had mutual diffusion in the bonding area, and the width of the diffusion layer was about 8 μ m。
(4) The phenomena of plastic deformation, melting and element diffusion exist in the interface of titanium / aluminum explosive welding, which shows that titanium / aluminum explosive welding has the typical characteristics of pressure welding, fusion welding and diffusion welding