According to the variety of base material and surface material, the common laminated layered Metal Composite plate sheet are copper/steel composite, aluminum/steel composite, stainless steel/steel composite, copper/aluminum composite, as well as precious metal composite plates such as molybdenum/titanium, pure silver/silver alloy.
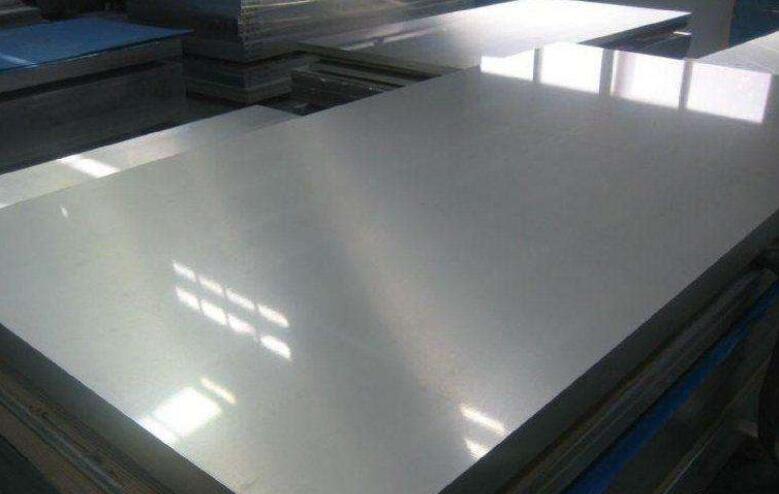
There are many composite processes for laminating different metals, such as explosive composite, hot-rolled composite, cold-rolled composite, bonded composite and so on.
1. Explosive recombination
Explosive recombination is a kind of metallurgical combination characterized by wavy interface, which makes use of the super-strong instantaneous force produced by explosive explosion to cause inclined collision between metals and forms hundreds of thousands of atmospheric pressure and effective thermal effects near the collision surface.
The main process of explosive recombination:
(1) Material preparation. Substrates need to be polished to remove scales and dirt; panels need to be straightened and cleaned.
(2) Explosive operation. It is divided into three main steps: laying board, laying explosives and detonating. The plywood can be directly stacked or the inner surface of the plywood can be placed at an angle according to the size of the area.
(3) After compounding. After composite annealing, the composite plate is leveled, and the quality of the bonding layer is detected by ultrasonic wave, and the product is graded.
The characteristics of explosive compounding: explosive compounding is easy to realize multi-layer compounding, and the bonding strength of composite interface is high; but the thickness of composite layer is uneven, and the precision of product is poor; the danger of production site is bad. Explosive compounding is suitable for the production of small batch, multi-variety and thick-gauge composite plates, and not suitable for mass production.
2. Hot-rolled composite
Hot rolling composite is a kind of metal base material and surface material overlapped together. After high temperature and high pressure rolling, the metal contact surface produces adhesion and friction behavior under the action of shear deformation force. It is a kind of metallurgical bonding between two materials to achieve fixation and thermal diffusion between metals.
Typical hot rolling process:
(1) Group billet. Two stainless steel plates (fabrics) with clean surface are overlapped between two carbon steel billets polished on the surface. The steel strips around the billets are sealed and welded to form composite slabs by vacuum pumping.
(2) Compound rolling. The composite slab is rolled according to the hot rolling process to reach the required thickness.
(3) Score neatness. The composite plate is divided into coils and finished by annealing, straightening and trimming, so that the composite plate meets the delivery conditions.
Hot-rolled composite features: high bonding strength; however, it is difficult to achieve surface cleanliness and high vacuum requirement when forming billets; compared with cold-rolled composite, the yield is lower, the surface quality of products is not high, and the metal with large difference in melting point can not be compounded.
3. Bonding Composite
Adhesive bonding is a combination of adhesives for the substrate and panel.
The technological process is: (1) surface cleaning, (2) surface brushing binder, (3) temperature compaction.
The characteristics of bonding composite are simple process, original brightness of material surface and good smoothness of product. However, it can not be bended at large angles or welded; it can not be used in high temperature or large temperature difference occasions.
4. Cold Rolling Composite