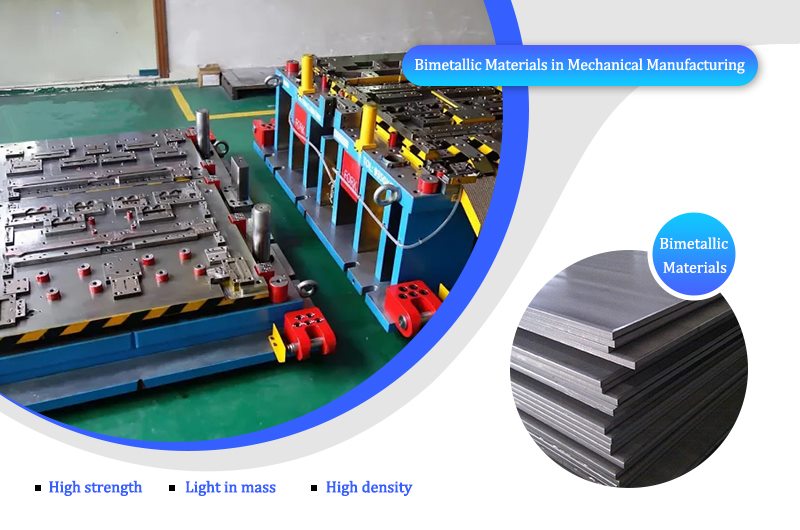
Points for attention in the selection of Bimetallic Materials in Mechanical Manufacturing
1.1 Economics of Material
Enterprise development attaches great importance to the ultimate economic benefits, so enterprises in the machinery manufacturing industry will use materials with higher cost performance, thereby reducing the production cost of enterprises and obtaining greater benefits under the premise of ensuring quality. In the process of selecting materials, enterprises will first understand the supply of materials, and secondly will consider material properties, prices, and processing costs, so as to reduce the cost of enterprises from the source.
1.2 Size and nature of loads
In the process of mechanical design, machinery manufacturing enterprises will consider the size and nature of material loads. The designer must consider whether the load size of the selected material meets the design requirements to ensure that the designed product will not have problems in use. Designers also need to consider other properties of the material to ensure that the product will not have quality problems in practical applications.
1.3 Dimensions and quality of components
In the process of mechanical manufacturing and production, the processing of some parts does not meet the design standards, which may easily lead to the size of the processed metal parts not meeting the actual production requirements, and the processed parts cannot be used. The processed metal composite material needs to be put into precision instruments, and the size and quality of the parts do not match the design, which will affect the quality of the finished product and the use value of the equipment. Therefore, machinery manufacturing enterprises must pay attention to the size and quality of parts in the actual selection of materials and material processing.
1.4 Working environment of parts
Different metal composite materials have different characteristics, and the working environment that mechanically manufactured products need to adapt to is also different. In a humid environment, the metal materials used must have strong corrosion resistance, and metal materials with corrosion resistance can be selected in the process of machining mechanical parts. In a high temperature environment, in order to ensure the normal operation of the equipment, materials with high temperature resistance are usually selected as mechanical parts. Therefore, designers of machinery manufacturing enterprises need to select suitable metal materials according to actual needs to adapt to different working environments.
2 Types of Bimetallic Materials in Mechanical Manufacturing
2.1 stainless steel clad steel
Stainless steel clad steel has many alloy composite materials, and there is a certain gap between such materials and traditional stainless steel materials. First of all, stainless steel clad steel has high corrosion resistance, which can not only resist daily chemical corrosion, but also effectively resist electrical corrosion. Because of its strong corrosion resistance, it is used in many fields. Secondly, stainless steel clad steel has good thermal conductivity, which also makes stainless steel clad steel one of the raw materials of coking equipment. By applying stainless steel clad steel, enterprises can not only ensure product quality, but also reduce product manufacturing costs. Finally, the decorative effect of stainless steel composite steel is better, and the appearance is usually white, which is in line with modern aesthetics.
2.2 carbon fiber graphite fiber composite material
Carbon fiber graphite fiber composite material is a composite material that combines carbon fiber and graphite fiber. This kind of composite material utilizes the repulsion characteristics of carbon fiber and man-made fiber during processing, so that carbon fiber graphite fiber composite material has the advantages of small expansion coefficient and high lubrication coefficient. Mechanical products made of carbon fiber graphite fiber composite materials have good heat resistance and corrosion resistance, which can ensure the effective use of mechanical products.
2.3 Metal Particle Plastic Composite Structural Materials
Metal particle-plastic composite structural materials have the characteristics of metal particles and plastic particles, and at the same time, this type of composite material is lighter in weight and higher in electrical conductivity. It is precisely because of these characteristics that metal pellet-plastic composite structural materials are used in various fields and become one of the more important composite materials in the machinery manufacturing industry.
2.4 Glass fiber composite structural materials
Glass fiber composite structural materials are widely used in the machinery manufacturing industry, and such composite materials have resin materials with high specific solidity inside. The addition of resin materials makes the glass fiber composite structure material have stronger hardness and resistance, and its stability is also enhanced, so it is used in mechanical products with a large degree of wear and chemical reactions.
2.5 Other types of Bimetal Materials
At this stage, there are still many types of metal composite materials under research and development. These types of metal composite materials are of high value and require a lot of research and development funds. Moreover, these materials are relatively expensive, and the production industry is not mature enough to be vigorously promoted. . For example, ceramic metal composite materials have the characteristics of high temperature resistance and corrosion resistance, and these metal composite materials are often used in bearing equipment; asbestos fiber composite materials are used in parts with sealing function because of their strong insulation, but these Special metal composite materials cost a lot and are often not valued by enterprises.
3 practical application of bimetal materials in mechanical manufacturing
3.1 manufacturing stamping dies
Stamping die manufacturing is the key of machine manufacturing, and machine manufacturing enterprises usually use metal composite materials to manufacture stamping dies. Metal composites have many advantages. In the actual stamping die manufacturing process, it is necessary to select the appropriate metal composites according to the actual situation to give full play to its performance and advantages. At this stage, in the process of mechanical manufacturing, the optional materials for stamping die manufacturing include blanking die materials, stretching die materials, cold extrusion die materials, etc. the requirements of each die material are different. In addition, the die needs to withstand large impact and friction when used, so only selecting appropriate metal composite materials can ensure the smooth progress of mechanical manufacturing. At the same time, machining is mostly carried out in high temperature environment, so it is necessary to choose a mold with high heat resistance in the manufacturing process of stamping die. Traditional stamping die manufacturing usually takes carbon steel material as the core. This material has high cost performance and strong plasticity, but its hardness is low, so it is difficult to bear the impact of daily production in the actual production process. Therefore, this type of material is not suitable for stamping die manufacturing at this stage. In recent years, the emergence of metal composites has made up for the lack of carbon steel materials. The quality of metal particle plastic composites is low, but it has strong hardness. At the same time, this kind of materials have high heat resistance and strong wear resistance. Applying it to the manufacturing of impact molds can obtain better results. In addition, carbon fiber and graphite fiber composites at this stage are widely used in impact mold manufacturing because of their strong high temperature resistance and corrosion resistance.
3.2 manufacturing mechanical parts
Metal composites have low expansion coefficient and high fatigue limit. These advantages make them not only used in the manufacturing of impact molds, but also widely used in the manufacturing of mechanical parts. The manufacturing of parts and components of mechanical products has relatively strict raw material selection standards. This set of standards has high requirements on the quality of parts and components, and also requires that parts and components can prolong the running time of machinery and prolong the service life of mechanical products. Therefore, in the actual selection process, we need to choose according to the actual working environment and requirements of mechanical products.
Traditional metal materials have the disadvantages of low strength and high coefficient of thermal expansion in the manufacturing of mechanical parts. For this, enterprises can make up for these defects by using metal composites. For example, in the manufacturing process of hammer crusher, the traditional hammer head material is ZGMn13, which has poor wear resistance, resulting in the short service life of mechanical products and the need for multiple maintenance; At present, the hammer crusher uses high chromium iron, high manganese steel and low alloy materials, which has great advantages and can effectively improve the bearing capacity of the hammer. Although the price of this type of material is higher than that of traditional metal materials, it has stronger wear resistance and can be used for a longer time. Compared with traditional metal materials, composite metal materials have strong conductivity, wear resistance and other characteristics, which can improve the comprehensive performance of mechanical products. In the actual manufacturing of mechanical parts, the application of metal composite materials can effectively prolong the service life of mechanical products and reduce the number of later overhaul and maintenance.
4. Better application of bi-metal materials in mechanical manufacturing
With the continuous advancement of the process of global economic integration, in recent years, the machinery manufacturing industry is also facing many challenges, which need continuous innovation and upgrading. In order to vigorously develop the machinery manufacturing industry in the new era, it is necessary to ensure the effective application of metal composites. Machinery manufacturing enterprises need to ensure the quality of metal composite materials in the processing process of metal composite materials, strengthen the management of raw material procurement, implement daily supervision and management, and avoid the quality of mechanical products failing to meet the standard due to the problems of raw materials. The development of China's machinery manufacturing industry has driven the development of China's comprehensive strength, and the application of metal composites is also closely related to the development of the times, which requires China's machinery manufacturing enterprises to innovate the manufacturing process of metal composites, constantly learn advanced knowledge, improve the manufacturing level of metal composites, and then realize the long-term development of metal composites in the field of machinery manufacturing. Machinery manufacturing enterprises need to keep up with the development trend of the times, pay attention to the application of metal composites in machinery manufacturing, and integrate metal composites and machinery manufacturing to achieve a win-win situation.
5 Conclusion
With the continuous improvement of the development level of China's machinery manufacturing industry, bimetal materials are more widely used, and the machinery manufacturing industry also pays more attention to the application of heavy metal composites in machinery manufacturing. Compared with traditional metal materials, metal composites have more obvious advantages and become the key materials in the manufacturing of mechanical parts and impact molds. In a word, the application of metal composites can further improve the performance of mechanical products, prolong the service life of mechanical products, and thus promote the development of China's machinery manufacturing industry.