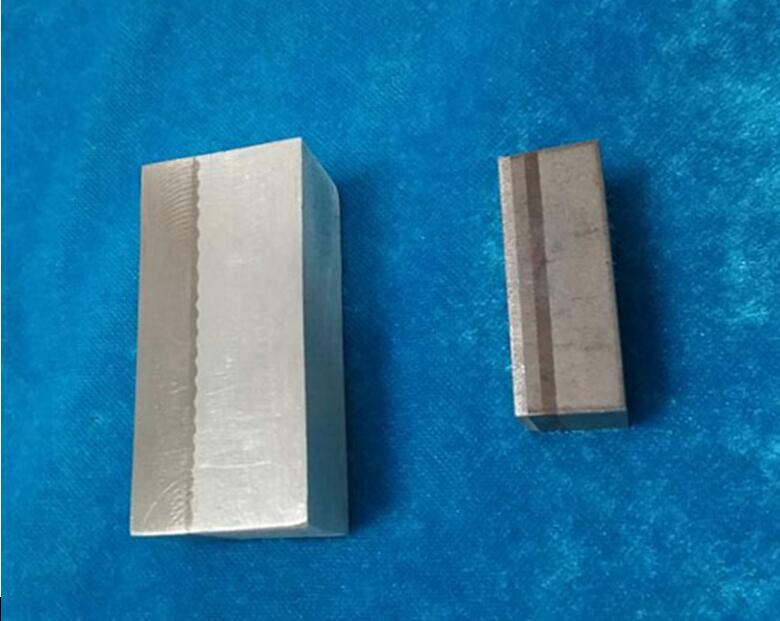
Aluminum stainless steel transition joints are mainly used in air separation units and closely related industries such as iron and steel, chemical industry (such as synthetic ammonia, large chemical fertilizer), petrochemical industry (such as PTA, ethylene) and coal chemical industry and other low temperature projects. It solves the welding (connection) problem between aluminum pressure vessel and stainless steel (or steel) pipeline and instrument nozzle in the above industry.
After the 1990s, many units in China, such as Northwest Research Institute of nonferrous metals, Northwest University of technology, Beijing Institute of Aeronautical Technology, Beijing Hongguang cable accessories factory, have adopted tube and rod explosive welding cladding; Friction welding of aluminum rod and copper (stainless steel) rod has been developed, but no breakthrough has been made. Both explosive welding and friction welding, aluminum and stainless steel are difficult to form diffusion miscibility except for the large difference in melting point. Secondly, the dispersion of intermetallic compound formed by the two makes the interface structure and joint properties worse, especially the welding between aluminum magnesium alloy (such as 5083) and stainless steel is more serious. At present, the explosive welding cladding of tube and rod can only be obtained Φ sixty πιπι The pressure bearing capacity of the reducers is low; It can be obtained by friction welding Φ eighty πιπι Copper aluminum joint below; For thick wall, large diameter aluminum stainless steel tubular transition joint welding, the above two methods are still helpless. At present, aluminum stainless steel tubular joints for air separation and other low temperature units still need to be imported from France and the United States
Chalco aluminum is a new kind of functional material and component which realizes metallurgical bonding of these two dissimilar metals with different melting point and properties in its cross section through special composite technology and strong spinning deformation process. Aluminum stainless steel transition joints have the characteristics of combining stainless steel ring with pure nickel transition layer; At the same time, it has the characteristics of aluminum ring, aluminum ring combined with pure titanium transition layer, pure nickel transition layer combined with pure titanium transition layer. The joint has a certain strength, especially at the interface of bimetallic, and can withstand the impact of pressure and temperature change (mainly from - 200 ℃ to room temperature); The pressure is usually 2 ~ 12MPa) and it can still keep good air tightness.